8 Tips for a More Efficient Warehouse
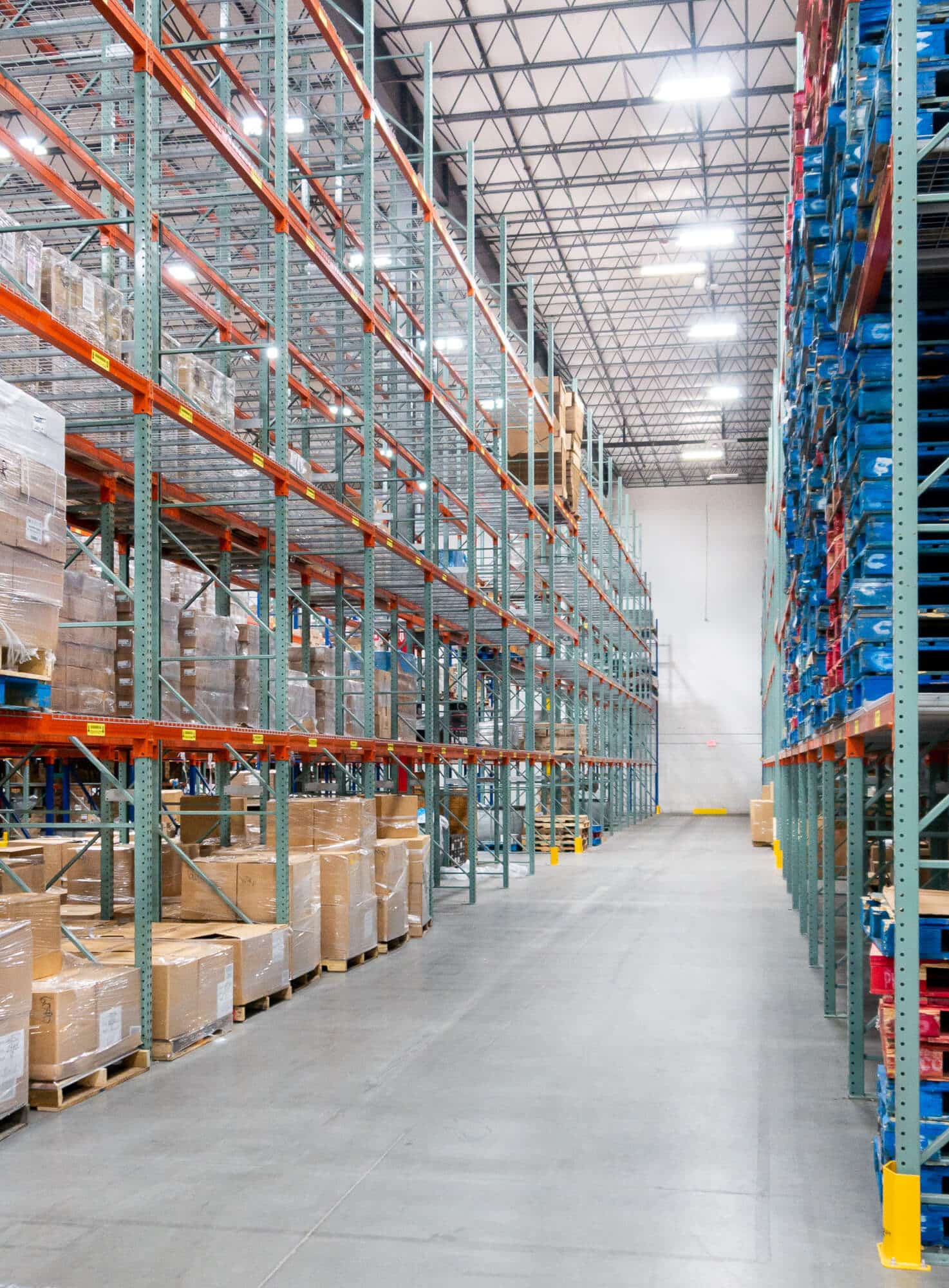
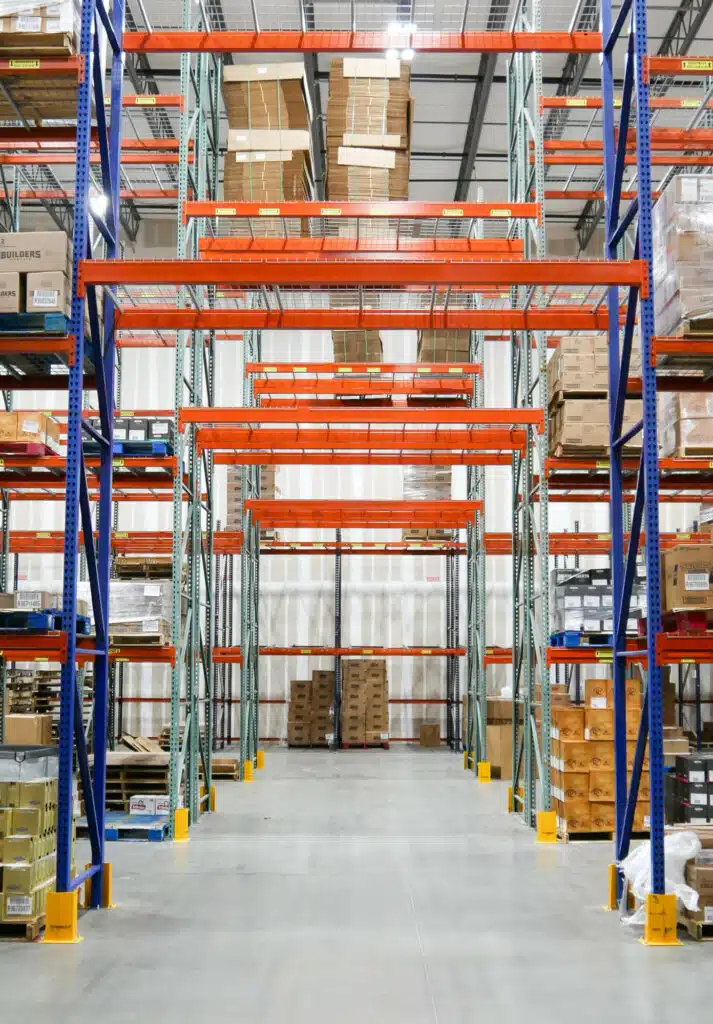
Introduction: Efficient warehouse management is crucial for businesses to streamline operations, reduce costs, and improve overall productivity. One key element in achieving optimal efficiency is the design and layout of the warehouse. A well-organized warehouse layout can significantly impact the speed and accuracy of order fulfillment. In this article, we will explore some top tips for designing the most efficient warehouse layout.
ABC Analysis for Inventory Segmentation: Implement the ABC analysis to classify inventory based on its importance. A-items are high-value and should be placed closer to the shipping area for quick access. B-items, with moderate importance, can be stored in a slightly less accessible area. C-items, lower in value, can be placed in more remote sections of the warehouse.
Utilize Vertical Space: Make the most of your warehouse’s vertical space by using tall shelving and storage systems. Vertical storage solutions help maximize floor space and provide additional room for inventory. Efficient use of vertical space also reduces the need for expansive warehouse facilities.
Optimal Aisle Width: Determine the right aisle width based on the type of equipment used for material handling. Narrow aisles can maximize storage capacity, but they may require specialized equipment such as narrow-aisle forklifts. Wide aisles provide easy access for standard forklifts, making them suitable for bulk storage areas.
Implement Cross-Docking: Cross-docking involves unloading products from incoming shipments and directly loading them onto outbound trucks with minimal storage time. This reduces handling and storage costs, speeding up the order fulfillment process. Plan your warehouse layout to include designated cross-docking areas.
Dynamic Slotting: Regularly review and adjust the placement of products in the warehouse based on their popularity and demand. Dynamic slotting ensures that fast-moving items are easily accessible, reducing the time it takes for employees to pick and pack orders.
Zone Picking System: Divide the warehouse into zones and assign specific employees or teams to each zone. This zone picking system helps streamline the order fulfillment process, as each team is responsible for picking items within their designated area. This reduces the need for extensive travel throughout the warehouse.
Use Technology for Automation: Incorporate warehouse management systems (WMS) and automation technologies to enhance efficiency. Automated storage and retrieval systems (AS/RS), conveyor systems, and barcode scanners can optimize order accuracy and reduce manual handling.
Consider Future Growth: Design the warehouse layout with future expansion in mind. Anticipate business growth and plan for scalability by leaving space for additional racks, shelving, and equipment. This foresight will save time and resources when the need for expansion arises.
Conclusion: A well-organized warehouse layout is essential for achieving maximum efficiency in logistics and order fulfillment. By implementing these tips, businesses can optimize their warehouse operations, reduce costs, and enhance overall productivity. Regularly reassess and update the warehouse layout to adapt to changing business needs and technological advancements in the field of warehouse management.
Overview: The 4 Core Components
- Uprights are vertical supports that form the primary framework of the system (shown in green)
- Beams connect directly to the uprights and act as the load bearing horizontal component of the system (shown in orange)
- Decking is placed over or into the beams to create a stable surface on which inventory can be placed (shown in blue)
- Safety equipment is crucial for preventing injuries, accidents and damage to products or the rack itself (shown in yellow)
Now let’s take a closer look at each of these components to gain a better understanding of their significance and impact on the functionality of your pallet rack system.
Upright Frames: Vertical Support
Pallet rack uprights are the vertical support columns that form the primary framework of the pallet racking system. Uprights consist of two vertical columns or posts welded to horizontal and diagonal braces. The weight of the stored pallets and goods is distributed through the uprights directly to the floor.
Quick Facts:
- The load-bearing capacity of uprights depends on their dimensions, material, and design.
- Uprights are available in a range of heights, allowing you to maximizing your available vertical space.
- Slots or holes are integrated into the uprights, allowing for the attachment of beams at varying heights.
- Uprights include built in footplates that should be securely anchored to the floor for stability
Beams: Horizontal Support
Pallet rack beams are the horizontal load-bearing components that span between the vertical upright frames of the rack system. They work in pairs and when combined create the “shelf” supports on which decking can be placed. Beams connect directly to pallet rack uprights via special slots or holes (as shown above).
When uprights and beams are connected, they form what are called storage bays, which is the formal term for the area where pallets and other items are stored within a pallet racking system.
Quick Facts:
- Pallet rack beams come in various widths and load capacities to accommodate an array
of storage requirements. - The most popular beam width is 8ft, allowing for two standard 48″ x 40″ pallets to be stored
side-by-side with ample clearance space. - The ability to adjust the beams along the height of the uprights gives you the flexibility to tailor the
rack to your specific storage needs. - There are various types of pallet rack beams, including step beams, box beams, and structural beams.
Choosing the right beam type depends on factors such as load capacity, application, and system design.
Decking: Storage Surface
Decking refers to the surface on which the pallets or products rest. It serves as an intermediate layer between the beams, creating a solid foundation on which inventory can be placed. The choice of decking material depends on factors such as weight, ventilation requirements, and fire safety regulations.
Quick Facts:
- Pallet rack decking comes in a range of materials, with the most popular option being wire mesh. Other options such as crossbars, bar grating, punch decking and perforated decking are great for a variety of specialty applications.
- Decking not only enhances the overall strength of the rack structure but also improves visibility, allows light to pass through, and prevents items from falling through the gaps between beams.
- Some types of pallet rack decking can impact the effectiveness of fire suppression systems. Before making a decision on what decking to install we recommend making sure it’s compliant with your local fire codes.
Safety Equipment: Protecting Personnel & Property
Pallet rack safety equipment, including rack guards, rack safety netting, guardrails, pallet backstops and rack safety clips are essential for maintaining a secure warehouse environment.
Safety equipment is a critical, and relatively low cost, way to protect your personnel and your property. It can typically be added
to your system during the initial installation process, or you can retrofit an existing system.
Quick Facts:
- Safety netting or wire mesh panels can be installed along the back of the racks to prevent items from falling and potentially injuring workers or damaging products in adjacent aisles.
- Rack guards are protective barriers or posts positioned at the ends of rack rows to prevent accidental collisions from equipment such as forklifts and pallet stackers.
- Column protectors are placed around the base of upright frames to shield them from potential impact by forklifts or other equipment, preventing damage and maintaining the structural integrity of the racks.
- Rack safety clips, also known as a beam locks or locking clips, are used to secure the connection between the horizontal beams and the vertical upright frames. They play a pivotal role in maintaining the stability and safety of the rack structure by preventing accidental dislodgment of the beams from the frames.
Thanks for reading! We hope you found this guide useful. If you have any additional questions about pallet racking or other material handling equipment, please contact us today – we’d be happy to help you!